FMEA / FMECA - Hata Modu ve Etkileri Analizi (Failure Mode and Effects Analysis- Failure Mode and Cr
- ÖZLEM ÖZDİLEK - A Sınıfı İş Güvenliği Uzmanı
- 21 Ara 2017
- 14 dakikada okunur
Güncelleme tarihi: 1 Nis 2022

Hata modu ve etki analizi (FMEA), 1950’lerin sonundan beri kullanılmakta olan ve en iyi kurgulanmış risk değerlendirme tekniklerinden biri olarak kabul edilmektedir. Yöntem iyi dökümante edilmiştir ve kullanılışı ile ilgili birçok açıklayıcı yayın ve standart mevcuttur.
Aşağıda bir uygulama görüyorsunuz:
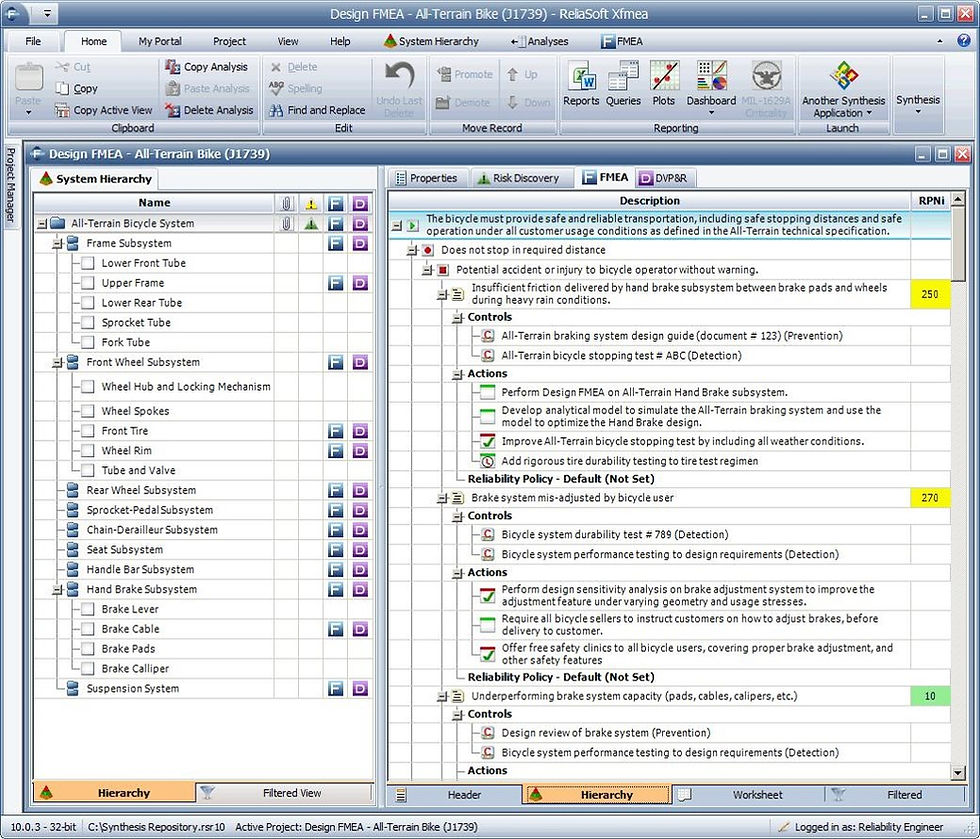
Hata modu ve etki analizi (FMEA), unsurlar, sistemler ya da süreçlerin planlanan hedeflerini gerçekleştiremediği hususları belirlemek için kullanılan bir tekniktir. FMEA metodu 60'lı yıllarda havacılık endüstrisinde kullanılmak üzere geliştirilmiştir. Bütün teknoloji ağırlıklı sektörler ile uzay sektörü, kimya endüstrisi ve otomobil sanayinde çok popülerdir. Bu metodun popüler olmasındaki başlıca sebep kullanımının kolay olması ve geniş teorik bilgi gerektirmemesidir.
Referans Standart :
IEC 60812, Sistem güvenilirliği için analiz teknikleri- Arıza modu ve etki analizine (FMEA) yönelik prosedürler (Analysis techniques for system reliability – Procedures for failure mode and effect analysis -FMEA)
FMEA metodu genellikle parçaların ve ekipmanların analizine odaklanır. Bu metod, başarısızlığın olabildiği yer ve alanların herbirini çözümler ve kişisel fikirleri de dikkate alarak değer biçer ve sistemin parçalarının herbirine uygulanabilir.
Hata Modu ve Etki Analizi uygulaması;
Her hatanın nedenlerini ve etkenlerini belirler,
Potansiyel hataları tanımlar,
Olasılık, şiddet ve saptanabilirliğe bağlı olarak hataların önceliğini ortaya çıkarır,
Sorunların izlenmesini ve düzeltici faaliyetlerin yapılmasını sağlar.
FMEA’nın birtakım uygulamaları bulunmaktadır: Unsur ve ürünler için kullanılan Tasarım (ya da ürün) FMEA, sistemler için kullanılan Sistem FMEA, üretim ve montaj süreçleri için kullanılan Süreç FMEA, Hizmet FMEA ve Yazılım FMEA. FMEA/FMECA, fiziksel bir sistemin tasarımı, üretimi ve işleyişi esnasında uygulanabilir. Ancak, sistemi geliştirmek için değişiklikler genel olarak tasarım aşamasında daha kolay gerçekleştirilir. FMEA ve FMECA, ayrıca süreçler ve prosedürler üzerinde de uygulanabilir. Örneğin, sağlık hizmetlerindeki medikal hataları ve bakım prosedürlerindeki hataları tanımlamak için de kullanılabilmektedir. Hata Modu ve Etki Analizi teknigi aşağıda sıralanan şekilde bir çok çeşitliliğe sahiptir ve uygulama alanları her türlü üretim ve hizmet şeklini kapsamaktadır.
Tasarım FMEA: Potansiyel veya bilinen hata türlerini tanımlayan, ilk üretim gerçekleşmeden hataların tanımlanması ve düzeltici faaliyetlerin uygulanmasını sağlayan bir yöntemdir.
Proses FMEA: Tasarım FMEA ve müşteri tarafından tanımlanmış olan kalite, güvenilirlik, maliyet ve verimlilik kriterlerini sağlamak için mühendislik çözümleri üretmeyi hedefleyen bir yöntemdir.
Hizmet FMEA: Müşteri hizmetlerini geliştirmek amacıyla üretim, kalite güvence ve pazarlama koordinasyonu ile uygulanan bir yöntemdir
Sistem FMEA: Bütün donanımların ve tasarımın tamamlanmasının sonrasında üretim, kalite güvence gibi sistemlerin akışını en elverişli hale getirmek için kullanılan bir yöntemdir.
Yapılacak olan bir FMEA tekniği uygulaması aşağıda özetlenmiş olan fonksiyonların gerçekleştirilmesini sağlar;
Proses ya da hizmette hataların oluşturacağı en küçük bir zararın bile oluşumunun engellenmesini sağlamak için hata türlerini sistematik olarak gözden geçirir,
Proses ya da hizmeti ya da bunların fonksiyonelliğini etkileyebilecek her türlü hatayı ve bu hatanın etkilerini tanımlar,
Tanımlanan bu hatalardan hangilerinin proses ya da hizmet operasyonlarında daha kritik etkilerinin olduğunu belirler, bu yüzden meydana gelebilecek en büyük hasarı ve hangi hata türünün bu hasarı üretebileceğini tanımlar,
Montaj, montaj öncesinde, proseste hataların oluşum olasılığını ve bunun nereden kaynaklanabileceğini (dizayn, operasyon, vb.) belirler,
Diger kaynaklardan elde edilmesi mümkün olmayan hata oranlarını ve türlerini tanımlayarak gerekli muayene programlarının kurulmasını sağlar,
Güvenilirliğin deneysel olarak test edilebilmesi için gerekli muayene programlarının kurulmasını sağlar,
Bir ürün için değişikliklerin olabilecek etkilerini tanımlar,
Yüksek riskli bileşenlerin nasıl güvenilir hale getirilebilecegini tanımlar,
Montaj hatalarının olabilecek kötü etkisinin nasıl giderilebileceğini tanımlar.
Girdiler:
FMEA ve FMECA, her bir unsur, ekipman, makine ya da proses parçasının başarı sağlayamadığı sistemlerinin analizleri için kullanılır. Bu analizi gerçekleştirmek için de, sistem unsurları hakkında detaylı bilgiye ihtiyaç duyar. Ayrıntılı bir Tasarım FMEA için söz konusu unsur ayrıntılı bağımsız bileşen düzeyinde olabilirken; yüksek düzeydeki Sistem FMEA için unsurlar, daha üst bir düzeyde tanımlanabilir. Bilgiler şunları içerebilir:
Analiz edilen sistemi, bileşenlerini ya da süreç aşamalarını içeren bir akış diyagramı ya da çizimler,
Bir sistem bileşeninin ya da sürecinin her bir aşamasının işlevinin kavranması,
İşleyişi etkileyebilecek çevresel ve diğer parametrelerin ayrıntıları,
Belirli arızalara yönelik sonuçların kavranması,
Mümkün olan yerlerde verileri ve arıza oranını içeren, arızalar üzerindeki tarihsel bilgi.
Süreç:
FMEA süreci aşağıda gösterilmiştir:
Çalışmanın kapsamı ve amaçları tanımlanır,
Takım üyeleri çalışma için bir araya gelir,
FMECA’e tabi olan sistem\sürec kavranmaya çalışılır,
Sistemin bileşenlerinde ya da aşamalarında meydana gelebilecek hatalar tanımlanır,
Her bileşenin ve aşamanın işlevi tanımlanır,
Listelenen her bileşen ve aşama için tanımlama yapılır,
Hatayı gidermek için, tasarımdaki doğal koşullar tanımlanır,
Şu sorular takım üyeleri tarafından tartışılır;
o Her bir bölümün hata yapma ihtimali mümkün müdür?
o Hangi mekanizmalar arızanın bu modlarını üretebilir?
o Eğer hata meydana gelir ise, hangi etkiler ortaya çıkabilir?
o Hata zararlı mıdır, zararsız mıdır?
o Hata nasıl ortaya çıkarılır?
FMECA için, çalışma grubu, tanımlanan hata modlarının her birini, kritikliklerine göre sınıflandırmaya devam eder. Bunun yapılabilmesi için bir takım yöntemler bulunmaktadır. Genel yöntemler aşağıda sunulmaktadır:
Mod kritiklik endeksi,
Risk seviyesi,
Risk öncelik sayısı.
Model kritikliği, dikkate alınan modun sistemin bir bütün olarak arızalanması sonucunu doğuracağı ihtimaline karşı bir önlemdir:
Hata etkisi ihtimali * Mod arıza oranı* Sistemin işleyiş süresi
Bu, bahsedilen ifadelerin nicel olarak tanımladığı durumlarda ekipman hatalarına sık olarak uygulanır ve bütün hata modları aynı sonuca sahiptir.
Risk seviyesi, hata ihtimali ile meydana gelen bir hata modunun sonuçlarının birleştirilmesi ile elde edilir. Değişik hata modlarının farklılaştığı ve ekipman sistemlerine ya da süreçlerine uygulandığı zaman kullanılır. Risk seviyesi kantitatif olarak, yarı kantitatif olarak ya da kalitatif olarak ifade edilir.
FMEA Analizine Daha Yakından Bakalım;
Hata Modu ve Etki Analizi, ürünlerin ve proseslerin geliştirilmesinde öncelikli olarak hata riskinin ortadan kaldırılmasına odaklanan ve bu amaçla yapılan faaliyetleri belgelendiren bir tekniktir. Bu analiz öncelikle önleyici faaliyetlerle ilgilenmektedir.
Olası Hata Türü ve Etkileri Analizi (FMEA); işletmedeki veya organizasyondaki önemli hata durumlarını belirlemek ve bu hataların işletmenin, çalışanların ve çevrenin güvenliği üzerindeki önemini değerlendiren ayrıntılı, sistematik ve dokümante edilen bir araştırma tekniğidir. 1960'lı yıllarda havacılık alanında ortaya konan bu yöntem, uzay ile ilgili çalışmalarda yer almış, daha sonraları nükleer, kimyasal, otomobil endüstrileri vb. endüstrilerde de kendini kabul ettirmeyi başarmıştır. Günümüzde en çok kullanılan yöntemlerden biridir.
FMEA disiplininin geçmişi diğer risk değerlendirme metodolojilerine oranla daha eskilere dayanır. Olası Hata Türü ve Etkileri Analizi (FMEA), ilk defa 9 Aralık 1949 tarihli ABD askeri prosedürü olan “Hata Türleri, Etkileri ve Riskinin Analizi Üzerine Prosedürler” diğer adı ile MIL –P- 1629 ile yayınlanmıştır. O dönemlerde Olası Hata Türü ve Etkileri analizi daha çok askeri amaçlı uçakların imalatı çalışmalarında kullanılmaktaydı. Daha sonra 1960-1965 yılları arsında ise NASA tarafından, APOLLO projesinde ilk defa uygulama alanı bulmuş ve yapılan uzay aracı çalışmalarında sistem ve ekipman hatalarının olasılıklarının belirlenmesinde kullanılmıştır. 1961 yılında ise ilk defa yine NASA tarafından ÇOK GİZLİ olarak niteledikleri FMEA analizinin ilk tabloları yayınlamıştır.
1975 yılında Japon NEC firması, FMEA disiplinin ilk endüstriyel uygulamasını başlatmıştır. 1980 yılında ise FORD firması tarafından otomotiv sanayinde uygulanmaya başlatılmış ve sistemde değişiklik yapılarak çok karmaşık olan askeri uygulama basitleştirilmiştir. Bu yöntem Fransız Renault ve Citroen otomotiv şirketince fransızca yazılımının baş harflarinin kısaltılmışı olarak, kısaca AMDEC (Analyse des Modes de Défaillances, de leurs Effets et de leur Criticité) olarak isimlendirilmiş ve otomotiv endüstrisinde uygulama imkanı bulmuştur.
Şubat 1993'te Otomotiv Endüstrisi Faaliyet Grubu (AIAG) ve Amerikan Kalite Kontrol Topluluğu (ASQC) endüstri çapında Hata Türü ve Etki Analizi standardı oluşturmuştur. Bu standartta Hata Türleri ve Etkileri Analizi'ni de içeren “İleri Ürün Kalite Planlaması” (Advanced Product Quality Planning - APQP) uygulamaya sokulmuş ve Kontrol Planı oluşturulmuştur. Bu standarttaki FMEA yapısı, QS 9000 standardının geliştirilmesinde işbirliği yapan Chrysler, Ford ve General Motors şirketleri tarafından büyük destek görmüş ve kabul edilmiştir.
TANIMLAR
FMEA disiplini çalışmasında geçen ve MIL-STD-1629 askeri standartında verilen tanımlamalar aşağıda verilmiştir;
Hata Türü ve Etkileri Analizi, FMEA (Failure Mode Effect Analysis): Bir sistemdeki, prosesteki, makinedeki veya techizattaki her bir potansiyel hata türünün sistem üzerindeki sonuçları ya da etkilerinin değerlendirilerek sıklıklarına göre sınıflandırılmaları temeline dayanan teknik analiz yöntemi.
Hata Türu Kritiklik Etki Analizi, FMCEA (Failure Mode Criticality Effect Analysis): Her bir potansiyel hatanın; analiz edilerek nasıl tespit edileceği ve hangi düzeltici faaliyetlerin başlatılacağına karar verme prosedürü.
Hata Tanımı (Failure Definition): Bir sistemde, proses veya techizatta istenmeyen durum yaratan ve performans parametreleri ile izin verilebilen limitler cinsinden açıklanan genel tanım.
Hata Nedeni (Failure Cause): Süreçlerden, tasarım hatalarından, malzemenin veya techizatın yanlış kullanılmasından, kalite eksikliklerinden ya da diğer süreçlerden kaynaklanan temel nedenler.
Hata Türü (Failure Mode): Hatanın oluşma yolu ve cihazın işlevi üzerindeki etkisi olarak tanımlanabilen bir hatanın gözlendiği durum. Sistemlerde arıza veya hatalara neden olan mekanizmalar, bir bütünlük içerisinde meydana gelen rastsal veya doğal olaylar olabilir.
Hata Etkisi (Failure Effect): Genellikle hataların etkileri, bütün sistemin hatadan nasıl etkilendiğine bağlı olarak sınıflandırılır. Bir hata türünün bir sistem biriminin operasyonu, fonksiyonu ya da çalışabilirliği üzerindeki sonuçları.
Çevre Etkisi (Environments Effect): Bir sistem, proses ve techizattan kaynaklanan ve malzemenin depolanması, kullanılması, taşınması, test edilmesi, kurulması ve kullanımı sırasında oluşan koşullar, etkiler, yayılımlar, atıklar ve bunların bir araya geldiğinde oluşturduğu çevresel etki.
Tek Hata Noktası (Single Failure Point) : Bir sistemde, operasyonel yöntemlerle ya da ekstra yapılan işlemlerle düzeltilemeyen bir birimin oluşturduğu hata.
Tespit Sistemi (Detection System): Normal çalışma koşullarında operatör tarafından ya da üretim elemanları tarafından, bir hatanın bazı özel tanıma faaliyetleriyle keşfedilmesini sağlayan yöntem.
Şiddet (Severity): Belli bir hata türü nedeniyle oluşmuş hatanın sonucu. Şiddet değerlendirilirken daima hatanın olabilecek en kötü sonucu düşünülür.
Kritiklik (Criticality): Bir hata türünün oluşum sıklığıyla ve etkisi ile ilgili bir ölçüm.
Kritiklik Analizi (Criticality Analysis): Hata türlerinin, hatanın önem ve oluşma olasılığı ile birlikte değerlendirilmesi.
Tespit Edilemeyen Hata (Undetectable Failure): Ekipman veya makinede, operatörün oluşan hatadan haberi olmasını sağlayacak herhangi bir tespit etme metodunun bulunmadığı durumlarda meydana gelen hata.
Çalışma Raporları (Study Reports): Sistemdeki olası hata türlerinin belirlenmesinde rehber olacak, tasarım sınırlamaları hakkında marjinal bilgileri veren rapor.
Blok Diyagramları (Block Diyagrams): Bir sistemdeki ekipmanların ve altsistemlerin birbirleriyle olan bağımlılığı, ilişkileri ile operasyonların sırasını göstermek için kullanılan diyagramlar.
Fonksiyonel Blok Diyagramları (Functional Block Diyagrams): Dizayn ve mühendislik akım şemalarında belirtilen operasyonlar ile fonksiyonların birbirleriyle olan ilişkilerini gösterir diyagram.
Güvenilirlik Blok Diyagramları (Reliability Block Diyagrams): Bir sistemin, prosesin, makinenin yada techizatın her birinin, çalışma koşulları içerisinde bütün fonksiyonlarının birbirleriyle bağlı oldukları ya da olmadıkları noktaların gösterildiği diyagramlar.
HTEA Raporu (FMEA Report): FMEA’nın sonuç tablosunun işlendiği ve diğer ilgili kaynak dokümanlarının, blok diyagramlarının, analiz yapılırken kullanılan tekniklerin ve sistemin tanımının da yapıldığı rapor.
FMEA Disiplini:
Sistem ve donanım hatalarının etkilerinin belirlenmesi için güvenilir bir değerlendirme tekniği olarak kullanılan FMEA disiplininde hatalar, görev başarısına ve personel/donanım güvenliğine etkilerine göre sınıflandırılmaktadır. Hata Türleri ve Etkileri Analizi, riskleri tahmin ederek hataları önlemeye yönelik güçlü bir analiz tekniğidir. Meydana gelebilecek önemli hata durumlarının belirlenmesine ve incelenmesine olanak sağlamak üzere, sistemlerin hata özelliklerinin pratik, gerçekçi ve dokümante edilmiş bir değerlendirmesinin yapılması sağlanır. FMEA disiplini süreçlerin, proseslerin ve organizasyonların geliştirilmesinde öncelikli olarak hata riskinin ortadan kaldırılmasına odaklanan ve bu amaçla yapılan faaliyetleri belgelendiren bir tekniktir, başarılı bir Hata Türü ve Etkileri Analizi uygulaması;
Her hatanın nedenlerini ve etkenlerini belirler,
Potansiyel hataları tanımlar,
Olasılık, şiddet ve saptanabilirliğe bağlı olarak hataların önceliğini ortaya çıkarır,
Sorunların izlenmesini ve düzeltici faaliyetlerin yapılmasını sağlar.
En yaygın kullanılan metodlardan biri olan FMEA çalışmasında, herhangi bir sistemin tamamı veya bölümleri ele alınıp, bunlardaki kısımlar, aletler, kompenentlerde ortaya çıkabilecek arızalardan hem bölümlerin hem de bütün sistemin nasıl etkilenebileceği analiz edilir.
Hata Türleri ve Etkileri Analizi öncelikli olarak organizasyon, sistem, proses ve ekipman geliştirme üzerine eğilen, disiplinli bir hata gözden geçirme tekniğidir, amaçları şunlardır:
Sistem veya proseste oluşabilecek potansiyel hataları önceden belirleyerek bu hataların oluşmasını engellemek,
Potansiyel hata türleri belirlendiğinde, onları ortadan kaldırmak için düzeltici önlemleri almak veya sürekli bir şekilde onların oluşma potansiyellerini azaltmak,
Montaj veya imalat süreci içinde, ekipmanlardan ve makinelerden kaynaklı tehlikelerin belirlenmesini sağlamak,
Mühendis veya teknik elemanların, deneyim ve geçmişteki problemlere dayanarak sistemde gördükleri muhtemel aksaklıkların analizini sağlamak,
Sistem, proses ve süreçlerdeki hataların oluşturacağı en küçük bir zararın bile oluşumunun engellenmesini sağlamak için hata türlerini sistematik olarak gözden geçirmek,
Sistem ve altsistemlerdeki süreçleri etkileyebilecek her türlü hatayı ve bu hatanın etkilerini tanımlamak,
Tanımlanan bu hatalardan hangilerinin proseste, süreçlerde, sistemde ya da operasyonlarda daha kritik etkiye sahip olduğunu belirlemek, bu yüzden meydana gelebilecek en büyük hasarı ve hangi hata türünün bu hasarı üretebileceğini tanımlamak,
Bir sistemin güvenilirlik derecesinin test edilebilmesi için gerekli verileri sağlamak,
Sistem eleman hatalarının, sisteme etkisi ile ilgili ayrıntılı bir FMEA yapılmadan önce, işletmenin önemli sistemlerinin işlevsel hata analizinin yapılması başarı oranını artıracaktır. Söz konusu sistemlerin birinde meydana gelen hatanın etkilerinin anlaşılmasını sağlamak amacıyla, sistemlerin birbirine bağımlı veya bağımsızlıkları blok diyagramları, hata ağacı, olay ağacı diyagramları vb. analizlerle araştırılır. Böylelikle, yalnızca işlevsel hata analizinde hata gösteren sistemlerin daha ayrıntılı bir FMEA ile araştırılması sağlanabilir.
Sistem Tanımı:
Aralarında aynı amaca yönelik ilişkiler bulunan öğelerin oluşturduğu bütüne sistem denir. Sistemler kendi içinde üçe ayrılır;
Manuel Sistemler: El işçiliğine dayanır. Basit el aletleri kullanılır ve süreç operatör tarafından kontrol edilir. Sistemin güç kaynağı, operatörün kendi fiziksel enerjisidir.
Mekanik(Yarı otomatik) Sistemler: Bu sistemler makinelerden kuruludur. Güç kaynağı makinelerdir, operatör ağırlıklı olarak makineler vasıtasıyla süreci kontrol eder.
Otomatize Sistemler: Bir sistemin tamamen otomatize olması için ya hiç ya da çok az insan gücüne ihtiyaç duyması gereklidir. Robotlar bu tip sistemlere bir örnek olarak gösterilebilir.
FMEA Çalışması:
Bir FMEA çalışmasındaki ilk aşama; iş akım şemaları ve makine ve techizat el kitaplarının kullanılması suretiyle, analiz edilecek sistemin ayrıntılı olarak incelenmesidir. Sistemin ve işlevsel gereksinimlerinin tanımı, aşağıdaki bilgiler dahil olmak üzere, bir liste halinde yapılmalıdır:
Sistemin çalışmasının ve yapısının genel tanımı,
Sistemin elemanları arasındaki işlevsel ilişki,
Her bir tipik işletim durumunda, sistemin ve onu oluşturan elemanların kabul edilebilir işlevsel çalışma sınırları, ve sistemdeki sınırlamalar.
Yüzde yüz hatasız sistemlerden söz etmek mümkün değildir, ancak sistemlerde yüksek güvenilirlik ancak yedekleme gibi tekniklerin kullanımıyla sağlanabilir. Düşük güvenilirlik düşük maliyetlerle elde edilir, fakat yenileme adımları ve kayıplar nedeniyle ek masraflar zorunlu hale gelebilir. Güvenilirlik arttıkça kayıplar azalıcak ve yenileme maliyetleri de düşecektir.
Eğer ana sistemler, herhangi bir olumsuz etki oluşturmaksızın hata durumu gösterirse, hatanın bir operatör tarafından algılanamadan devam etme durumu hariç, daha ayrıntılı değerlendirmeye gerek yoktur.
Sistemin Blok Diyagramlarının Oluşturulması:
İkinci aşama; gerek sistemin işlevlerinin ve çalışmasının teknik olarak anlaşılması, gerekse daha sonraki analizler için, sistemin işlevsel akış sırasını gösteren blok diyagramlarının oluşturulmasıdır. Blok diyagramı asgari olarak aşağıda belirtilenleri içermelidir:
Sistemin ana alt sistemler veya teçhizat olarak kısımları,
Her bir alt sistemin devamlı olarak izlenebileceği sınıflandırılmış tüm girdi ve çıktılar ve belirleyici numaralar,
Hatalara karşı otomatik koruma önlemleri sağlayan tüm destekler, seçenekli sinyal düzenleri ve diğer mühendislik özellikleri.
Olası Hata Türü:
Hata, kısaca bir birimin sahip olması gereken özelliklerinden bir sapma olarak tanımlanır. Bir sistem, bir ürün için hata, istenen işlevlerini yerine getirememe durumudur. Bu durumda genelleştirilmiş ifadeyle hata “tanımlanan işlevlerini yerine getirme kabiliyetindeki kayıp” olarak tanımlanabilir.
Genellikle hatanın görülme biçimi, teçhizat veya sistem üzerindeki etkisini tanımlar. Her sistem, işlevsel çıktıdan başlayarak, bütünsel bir yaklaşımla değerlendirilmeli ve her hatanın herhangi bir andaki olası bir nedenden kaynaklandığı kabul edilmelidir. Bir hata durumunun birden fazla nedeni olabileceğinden, her hata durumu için olası tüm bağımsız nedenler belirlenmelidir.
Sistemin görevini tam anlamıyla yerine getirememesi hata, bu hatanın ortaya çıkma şekli ise hata türüdür. Olası hata türü, hatanın ortaya çıkma durumunu ve sistemi etkilemesinin tanımını içerir. Hata türünü belirlemek için, “makine ya da süreç istenilmeyen durum veya tehlikeyi nasıl yapar ” sorusuna cevap aranır. Ortaya çıkabilecek hata türleri fonksiyonellik veya donanımla ilişkili olabilir. Hata türü çeşitleri aşağıda verilmiştir;
Hata durumunun işletme, işlev veya teçhizatın veya sistemin durumu üzerindeki sonuçları "hata etkisi" olarak adlandırılır. Belirli bir alt sistem veya teçhizat üzerindeki hata etkisi "Lokal Hata Etkisi" olarak tanımlanır. Lokal hata etkilerinin incelenmesi, sistemin o düzeydeki destek teçhizatının veya düzeltici çalışmaların etkinliğini belirlemede yardımcı olacaktır. Bir teçhizatın veya alt sistemin hatasının, sistem çıktısı (sistemin işlevi) üzerindeki etkisi "Sonuç Etkisi" olarak tanımlanır. Eğer bir hatanın sonuç etkisi, tehlikeli veya felaketsel olarak sınıflandırılıyorsa, bu etkiyi önlemek veya en aza indirmek için genellikle destekleme teçhizatı gereklidir.Olası Hataların Etkileri:
Olası Hata Etkileri belirlenirken, hata gerçekleşirse ne olacak sorusuna cevap aranır ve ekipmanı veya makineyi kullanacak operatörün veya çevrenin bundan nasıl etkileneceği belirlenmeye çalışılır.
Olası Hata Sebebi:
Listelenen hata türleri ve etkilerinden sonra, bu hatalara sebep olan koşulların belirlenmesi gereklidir ve genel olarak bu, hata türünü oluşturan ilk anormalliktir. Bu listeleme sırasında kesin olarak belirli yani açık sebepler yazılmalıdır, belirsiz ve kesin olmayan sebepler yazılmamalıdır. Hata türünün olası sebeplerini tanımlamak için, beyin fırtınası, sebep-sonuç diyagramları, hata ağacı analizleri kullanılır.
Sistem elemanlarının hataları algılanamaz tipte ise (yani gizli bir arıza veya kullanıcıya görsel veya sesli herhangi bir sinyal vermeyen bir hata) ve sistem çalışmasına devam edebiliyorsa, analiz algılanamayan ilk hata ile birlikte olması halinde daha şiddetli etkilere örneğin; tehlikeli veya felaketsel etkilere neden olabilecek olan ikinci bir hatanın etkilerini belirleyecek şekilde genişletilmelidir.
Fonksiyonların Tanımlanması:
Herhangi bir sistem çevresi ile çeşitli şekillerde temastadır. Sistem kendi ana fonksiyonlarını yerine getirirken aynı zamanda çevrenin baskısıyla yaptığı bazı işlevleri de yerine getirmektedir. Ana fonksiyonlara, akış fonksiyonları da denebilir, çünkü sistemin başından sonuna kadar kontrollü akışa uyum sağlarlar. Sistemi oluşturan parçaların temel fonksiyonları ise dizayn fonksiyonlarıdır.
Fonksiyonel Blok Diyagramlar:
Fonksiyonel Blok Diyagramları, fonksiyonların birbirleriyle olan ilgilerini anlamaya yardımcı olan, dış çevre, sistemin parçalarının her biri, iş akışları, iç dizayn ve akışları, sistem elemanları arasında gerçek veya gayri resmi ilişkileri gösteren diyagramlardır.
Blok diyagramlar, fonksiyonel parçaların karşılıklı ilişkilerini, birbiriyle olan bağımlılıklarını ve operasyonları tanımlayarak FMEA yönteminde kullanılan ekipmanların tüm seviyelerinde, hata modlarının etkilerini takip etmemizi sağlar. Bunlar operasyonların bağımlı veya bağımsız olduğunu göstermektedir.
Hata Ağacı Analizi İle Birlikte Kullanım:
FMEA uygulanması gereken karmaşık sistemlerde Hata Ağacı Analizi (FTA)’dan faydalanılır. FTA, sistemin çalışmasını engelleyecek bütün durumların şematik olarak dallandırma yapılarak tanımlanmasını içeren sistematik bir tekniktir. Dizayn performansından çok sistemin hangi şartlarda çalışmayacağını inceler.
Analiz Sonuçlarının Değerlendirmesi:
Bu aşamada her bir olası hatanın risk esasına göre kritiklikleri belirlenir. MIL-STD 1629A (1984)'da kritiklik "Hata türü ve onun ortaya çıkma sıklığının sonuçlarının göreli ölçüsüdür" şeklinde tanımlanmaktadır. FMEA yöntemi diğer risk analizi teknikleri gibi, girdi olarak sayısal verilere (olasılık, şiddet, keşfedilebilirlik) ihtiyaç duyar. Kritikliği belirleyen ölçüt “Risk Öncelik Sayısı- RÖS”dır. Uygulamada işlem kolaylığı sağlamak amacıyla kritiklik, olasılıksal bir değerler yerine sayısal büyüklük olarak ifade edilir. Risk öncelik sayısı aşağıdaki formülasyonla bulunur;
P: Her bir hata modunun oluşma olasılık değeri;
S: Hatanın ne kadar önemli olduğunun değeri,
D: Hataların keşfedilmesinin zorluk derecelendirilmesi,
RÖS = P(olasılık) x S(şiddet) x D(fark edilebilirlik)
Ancak pek çok durumda hazır veri mevcut değildir veya mevcut veriler yeterli ve güvenilir değildir. Bu durumda, çoğu kez sayısal veriler mühendis veya teknik elemanların yargısına başvurularak tahmin edilmektedir. Onlu skalada puanlamada FMEA takımının konu ile ilgili bilgi seviyesi ve deneyimleri nedeniyle ciddi sapmalar olmakta, uzlaşım güçlüğü yaşanabilmektedir. Kişiler değerlerini sayısal olarak ifade etmekten çok, niteliksel olarak ifade etme eğilimi göstermektedirler, yani çoğu kez bu yolla elde edilen veriler sayısal değildir.
FMEA çalışmasında Risk Öncelik Sayısının bulunmasında özellikle puanlama ile ilgili olarak yapılan birçok kabul FMEA yönteminin zayıf yönlerinden biridir. Bu noktalarda geçmiş tecrübeler ve ekibin konuya yaklaşımı büyük önem taşır ve yapılanlar kısmen subjektif değerlendirmelerdir. Mühendis ve teknik eleman yargısına dayanılarak elde edilen bilgiler, niteliksel olma özelliğinden dolayı, bir dile ait sözcükler ve deyimler (az, çok az gibi) ile ifade edilen “bulanık bilgiler”dir. Bu iki eksikliğin giderilebilmesi için, FMEA’nın olasılık teoremleri ile ele alınması önerilmektedir.
Olasılık:
Öncelikle hata ve sebep olasılığı belirlenmeye çalışılır. Hata türünün ne sıklıkta oluşabileceği hesaplanarak olasılık bir ila on arasında derecelendirilir. Grup üyelerinin bilgi birikimi ve tecrübelerine göre derecelendirme yapılır. Hata türünün oluşma sıklığı dikkate alınır ve olasılık derecelendirme tablosu kullanılır. Benzer bir proses varsa, buradaki istatistiki bilgilerden yaralanılır.
Her bir nedenin, hata türünün oluşmasındaki katkısı olasılık teoremleri ve istatistiksel yöntemlerle veya benzer ürünlerin verilerinden yararlanılarak belirlemek mümkündür. Veri tabanları oluşturulmamışsa ve hesaplama yöntemleri kullanılamıyorsa, grup üyelerinin deneyimlerinden yararlanılarak olasılık değerlerini kestirmeleri istenir.
Şayet veri var ise “ Cpk -Makine Yeterliliği” ile olasılık değeri tayin edilebilir. Proses Yeterlilik Analizi prosesteki doğal varyasyonun ölçümünü içerir. Proses yeterliliği, prosesteki varyasyonun bir fonksiyonudur ve prosesteki altı standart sapma yayılımı olarak tanımlanabilir. Proses varyasyonu ve spesifikasyonları karşılaştırmak için kullanılan iki indeks, Cp ve Cpk değerleridir.
Bir ekipmanın belirli özelliklerini yanılgıya meydan vermeyecek açıklıkta tanımlayan değerlere “Spesifikasyon” denir. Herhangi bir spesifikasyonun sahip olduğu toleranslarının oluşturduğu değerlere de “Spesifikasyon Limitleri” denir.
Normal dağılımlar için proses yeterliliğinin belirlenmesi için Cp ve Cpk olarak isimlendirilen proses yetenek indeksleri kullanılır. Bunlardan Cp indeksi prosesin sadece yayılımını kontrol ederken, Cpk indeksi ise prosesin hem yayılımını, hemde ortalamasının hedeflerden sapmasını kontrol etmektedir. Cp ve Cpk indeksleri, proses yeteneğinin uygunluğunun sayısal olarak değerlendirilmesidir.
ÜSL : Üst Spesifikasyon Limiti
ASL : Alt Spesifikasyon Limiti
( ÜSL - ASL ) : Spesifikasyon aralığı
s : Standart sapma
X : verilerin aritmetik ortalaması
Cp,Cpk: Makine yeterlilik indisleri (Cp dağılımın konumu, Cpk dağılımın konumu ve sapması hakkında bilgi sağlar.)
Cm,Cmk : Makine yeterlilik indisleri (Cm dağılımın konumu, Cmk dağılımın konumu ve sapması hakkında bilgi sağlar.)
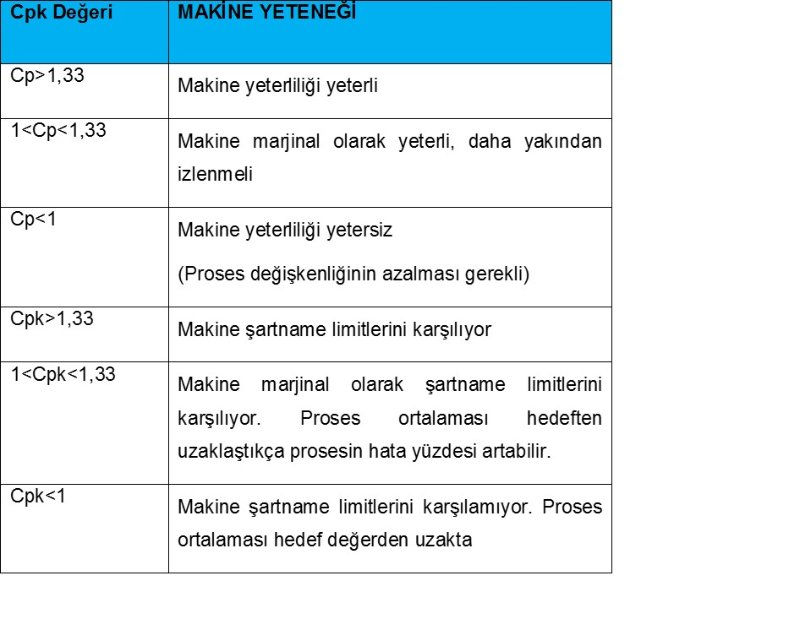
Makine yeterlilik indislerinden küçük olan değerlendirilir. Makinenin yeterli olması için indis minimum 1 olmalıdır. Ancak birçok dokümanda prosesin zaman içindeki muhtemel sapmaları da dikkate alınarak bu oran 1,33 verilmektedir.
Cpk indisi ise, proses ortalamasının hedef değere göre konumunu ve spesifikasyon limitleri arasındaki konumunu gösterir. İndekslerin değerlerine göre Proses yeteneğinin sayısal ifadesi aşağıda verilmiştir;
Eğer proses veya makineler, istatistiksel süreç kontrol altında ise ya da istatistiksel süreç kontrol teknikleri ile izlenen daha önceki bir sürecin benzeriyse, olasılığın değerlendirmesi için istatistiksel veriler kullanılmalıdır. Bu durumda FMEA takımının Cpk – Proses Yeterlilik İndisine göre karar vermeleri doğru olacaktır, ayrıca söz konusu değerlendirme subjektif bir değerlendirme olmaktan kurtulacaktır.
Olması muhtemel hata türünün sisteme, ekipmana, süreçe, personele ve çevreye olan etkisinin önemini derecelendirmede kullanılır. Personele olan etkisi açısından hatanın etkisi bir ile on arasında derecelendirilir. Bu dereceler hata türlerinin etkisiyle bağlantılıdır. Benzer etki yaratan hatanın aynı şiddet değeri almasına dikkat edilir.
Şiddet:
Şiddet derecesini belirlemek için kullanılan veri kaynakları hata etkisini belirlemede kullanılanlarla aynıdır. Hata ağırlığını belirlemek için daha önce meydana gelmiş olayların sonucundan, geçmiş dönemlerde benzer sistemler için tutulan kayıtlardan, laboratuar deneyleri veya simülasyon çalışmaları sonuçlarından ve analizi gerçekleştiren kişilerin deneyimlerinden yararlanılır. Hata şekillerinin olası sonuçlarını, niteliksel bir ölçü ile değerlendirebilmek amacıyla sınıflandırma yapılır. Şiddet sınıflandırması olarak adlandırılan bu sınıflandırmada analiz edilen her birimin veya sistemin hata türünün sonuçlarının kayıp ile ifadesidir. Kayıplar sistemin hasar görmesi, fonksiyonunu yitirmesi can kaybı, yaralanma ve çevresel etki şeklinde ortaya çıkar. Kayıp miktar ve çeşitleri, hata etkisinin derecesini belirler.
Fark Edilebilirlik:
Hataların fark edilebilme olasılığıdır.
Potansiyel bir hatanın,
Burada da yine bir ile on arasında derecelendirme uygulanır.
Olası hatanın, bir sonraki aşamada veya işletim esnasında personel tarafından tespit edilebilmesinin olasılığıdır. Bu nedenle, keşfedilebilirlik ile ilgili olasılık değeri, ortaya çıktığı varsayılan hata nedeninin ya da şeklinin personel tarafından saptanabilme olasılığı olarak tanımlanır. Keşfedebilirlik personelin hatayı saptama olasılığına göre bir ila on arasında derecelendirilir. Olasılık değerleri, analiz edilen birimlerin benzerlerinin, geçmiş dönem verilerinden, iç denetlemelerinden bulunabilir. Olasılık durumu kestirilemediği durumlarda, bir değer verebilmek için grup üyelerinin deneyimlerine başvurulur.
Sonuçların Değerlendirilmesi:
Genel kabul görmüş değerlendirme olarak, RÖS değerlerine göre düzeltici önlem alma kararları şu şekilde verilir;
RÖS < 60 ise önlem almaya gerek yoktur.
60 ≤RÖS ≤100 ise önlem alınması gerekir.
RÖS > 100 ise acil önlem alınması gerekir.
RÖS değerinin almış olduğu değere göre, olası hata şekillerini veya nedenlerini ortadan kaldırmak veya olumsuz etkilerinin en aza indirilmesi için tasarım, üretim süreci, malzeme veya üretim yöntemi gibi çeşitli unsurlarda değişiklik önerilir. Bunun için olasılık, şiddet ve keşfedilebilirlik değerlerini azaltmak gereklidir.
SONUÇ OLARAK; Düzeltici Önlemler
Teknolojinin gelişmesi ve hatalarda görülen artış ile birlikte hataların önlenmesine yönelik anlayışlar da zaman içerisinde büyük değişim göstermiştir. Hata meydana geldikten sonra ıskartaların gözlenmesi, güvenirliğin ortaya konulması ve problemlere çözüm üretilmesinin yeterli sonuç getirmediği görülmüş ve bu reaktif uygulamalardan vazgeçilerek proaktif uygulamalara geçilmiştir. Yeni düşünce çerçevesinde ıskartaların önüne geçilmesi, güvenilirliğin ve kullanılabilirliğin artırılması ve problemlerin önlenmesi gibi proaktif uygulamaların yapılmasının, hataların önlenmesinde en büyük düzeltici önlem olduğu kabul edilmiştir.
KAYNAKÇA
ÖZKILIÇ, Ö.,İş Sağlığı ve Güvenliği Yönetim Sistemleri ve Risk Değerlendirme Metodolojileri, TISK, Ankara, Mart, 2005
Özkılıç, Ö., İş Sağlığı, Güvenliği ve Çevresel Etki Risk Değerlendirmesi; MESS, İstanbul, 2007
25 Nisan 2013 tarih ve 28628 sayılı İş Ekipmanlarının Kullanımında Sağlık ve Güvenlik Şartları Yönetmeliği
Özkılıç, Ö., Risk Değerlendirmesi, ATEX Direktifleri-Patlayıcı Ortamlar, Büyük Endüstriyel Kazaların Önlenmesi ve Etkilerinin Azaltılması, Kantitatif Risk Değerlendirme, Seveso II ve Seveso III Direktifi (COMAH Direktifi), TİSK, Yayın No:338, 2014
03.03.2009 tarih ve 27158 sayılı Makine Emniyeti Yönetmeliği
28.09.2014 tarih ve 29133 sayılı Makine Emniyeti Direktifinde Değişiklik Yapılması Hakkında Yönetmelik
25.04.2013 tarih ve 28628 sayılı (Son Değ.23.07.2016/29779) İş Ekipmanlarının Kullanımında Sağlık ve Güvenlik Şartları Yönetmeliği
Comments