
Özlem Academy Education Consultancy Inc.
CONTACT US FOR YOUR QUESTIONS
Address : Tatlısu Mah. Pakdil Sok. PERSPECTIVE Plaza No:5 Floor:1 Flat:3, Şerifali Cd., 34774 Umraniye/Istanbul
Tel Office: +90 (216) 594 55 25
Mobile: +90 (533) 380 83 72
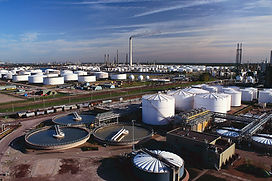
Our services
MAPP - MAJOR ACCIDENT PREVENTION POLICY DOCUMENT
PREPARATION SERVICE
With our expert staff, we offer the highest quality Major Accident Prevention Policy Document preparation service.
You can entrust us with the preparation of your "Major Accident Prevention Policy Document" within the scope of the Seveso Directive!
What is the Seveso Directive?
The Seveso directive is a European Union regulation that aims to reduce possible risks during the use and storage of hazardous chemicals in businesses. This directive aims to manage the effects of accidents caused by hazardous materials in large-scale industrial plants.
Requirements and Application:
-
Businesses should make their own risk assessments based on the amount and characteristics of hazardous chemicals.
-
Businesses should identify hazard scenarios and develop contingency plans.
-
As a result of risk assessments, the security measures to be taken should be determined.
-
Businesses must publicly report their facilities within certain limits.
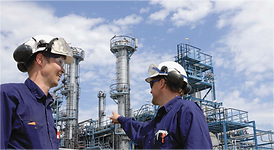
Major Accident Prevention Policy Document We Prepare in the Best Way.
"We are with you to be safe."
Major Accident Prevention Policy Document
MADDE 10 – (1) The operator of the lower-level organization prepares or has prepared the major accident prevention policy document by taking into account the information requested in the regulation on the major accident prevention policy document and the safety management system specified in Annex-3. The major accident prevention policy document is a document containing information about the safety management system specified in Annex-3 with the aim of preventing major industrial accidents and taking high-level protection measures at the workplace.
The major accident prevention policy document includes the following subsections:
Introduction of the Organization and Facilities in the Organization
1.1. Introduction of the Organization
1.1.1. The organization has a registered registration number in the Social Security Institution.
1.1.2. Determined based on the date of issuance of the Major Accident Prevention Policy (MAPP) document, the number of male and female employees and the number of shifts are specified
1.1.3. A satellite image showing the boundaries and surroundings of the area where the organization is located is provided.
1.1.4. Summary information is provided on the main activities and production of the organization.
1.1.5. A copy of the "Organization Information" page in the notification system of the Ministry of Environment and Urbanization and the declaration of the notification are provided.
1.2. Site Plan of the Organization
A scaled site plan of the entire organization is provided. Facilities with a risk of major accidents are marked.
1.3. Introduction of Facilities in the Organization
1.3.1. General Information about the Facilities in the Organization
Information is provided about the number of facilities, their names, the number of employees, dates of commissioning, capacities, process relationships, and planned shutdown periods.
1.3.2. Detailed Information about the Facilities in the Organization
For each facility:
a) Appropriate process flow diagram,
b) List of hazardous substances processed and equipment information,
c) List of critical equipment and control loops,
d) Types and capacities of storage are provided.
1.3.3. Information on the Layout of Facilities
Information about storage, process, control rooms, security systems, and entrances is provided on plans.
1.3.4. Information on Explosion and Fire Fighting Measures
Measures taken against fire/explosion hazards and potential ignition sources are described.
1.3.5. Information on Measures Against the Spread of Accidents
Measures taken against the spread of major accidents are explained.
1.3.6. Other Information
Detailed information is provided about measures taken for the processing, storage, process conditions of hazardous substances, and environmental factors.
1.4. Hazardous Substances in the Organization
Information about hazardous substances in the organization is presented in accordance with the sample table.
Information about the Organization's Safety Management System
The Safety Management System (SMS) is the totality of technical and organizational activities to prevent major industrial accidents and reduce their impact. The SMS is created by lower-level organizations and includes specified elements. These elements are organization and personnel, identification and evaluation of major accidents, operational control, change management, planning for emergencies, monitoring of performance, and audit and review.
2.1. Safety Management System (SMS)
2.1.1. Organization and Personnel
The organization's structure and the unit responsible for process safety are specified. The duties of personnel and the individuals to be replaced in case of temporary absence are explained. In addition, the responsibilities of personnel involved in preventing major industrial accidents and communication channels to subcontractor employees are specified.
Methods used to promote a safety culture and ensure regular participation of subcontractor employees are provided.
Information is provided on personnel training on preventing major accidents, training needs, and methods of exchanging safety information.
2.1.2. Identification and Evaluation of Major Accident Hazards
The process of identifying and evaluating major accident hazards is detailed, explaining the methodology used and data sources.
2.1.3. Operational Control
Information is provided on operational steps such as commissioning of the facility, operational stages, and decommissioning of process equipment.
2.1.4. Change Management
Change management ensures effective management of critical changes that occur within the organization.
2.1.4.1 Critical Changes
Critical changes are changes that significantly affect the functioning of the organization and must be carefully identified based on specific criteria.
2.1.4.2 Content of Critical Changes
A method is established for organizational, personnel, process, hazardous substance storage, equipment, and safety document changes, as well as changes related to environmental conditions. Each change stage includes details such as need, nature, and team roles.
2.1.4.3 Identification of Hazards Arising from Changes
Information is provided on methods for identifying hazards that may arise during and after the change process and methods for eliminating them.
2.1.4.4 Recording Changes and Updating Documents
A specific procedure is followed for recording changes made and updating relevant documents.
2.1.4.5 Informing Employees
Detailed information is provided on the process of informing employees and relevant parties when a critical change occurs.
2.1.5. Planning for Emergencies
When preparing the internal emergency plan, the operator includes the following information:
a) Criteria for determining emergencies.
b) Establishment of emergency organizations and criteria for determining responsible persons.
c) Training and information activities for employees, subcontractor employees, visitors, and emergency response teams.
ç) Review of emergency drills, identification of deficiencies, and corrective actions.
2.1.6. Monitoring Performance
Performance monitoring includes the following information:
a) Methods for setting specific, measurable, achievable, and time-bound goals for Safety Management System elements.
b) Criteria for determining compliance with established goals and the frequency of review.
c) Methods for reporting non-compliance with established goals and identifying corrective actions.
ç) Methods for reporting major accidents and near-miss incidents, and methods for communicating corrective and preventive actions to employees.
2.1.7. Audit and Review
Information is provided about regular internal audits to be conducted at intervals not exceeding two years:
a) Criteria for identifying persons to conduct internal audits.
b) Authorities and responsibilities of persons conducting internal audits.
c) Methods used in conducting internal audits and reporting audit results.
ç) Methods for informing senior management of audit results.
To get a detailed idea about Quantitative Risk Assessment and SMS, please review the Article and Blog section.

Employer's Obligation to Take Action
Regulation on Preventing Major Industrial Accidents and Reducing Their Effects
Article 6:
General Obligation of the Operator
The operator is obliged to take all necessary measures to prevent major accidents and, in cases where it cannot be prevented, to limit their effects in a way that causes the least damage to the environment and people.